What is Resource Utilization?
Resource utilization refers to the effective deployment and management of various resources to achieve optimal outcomes. Imagine a scenario where a software services organization is facing a surge in client projects with varying deadlines and resource requirements. They must allocate their software development teams, assign tasks, and manage project resources effectively to ensure timely delivery, optimal utilization of skills, and client satisfaction. Effective resource management is crucial to balance workloads, meet project goals, and maintain the organization’s reputation for delivering quality software solutions. Resource utilization underpins the operational efficacy across a spectrum of industries.
At its core, resource utilization refers to the effective deployment and management of various resources to achieve optimal outcomes.
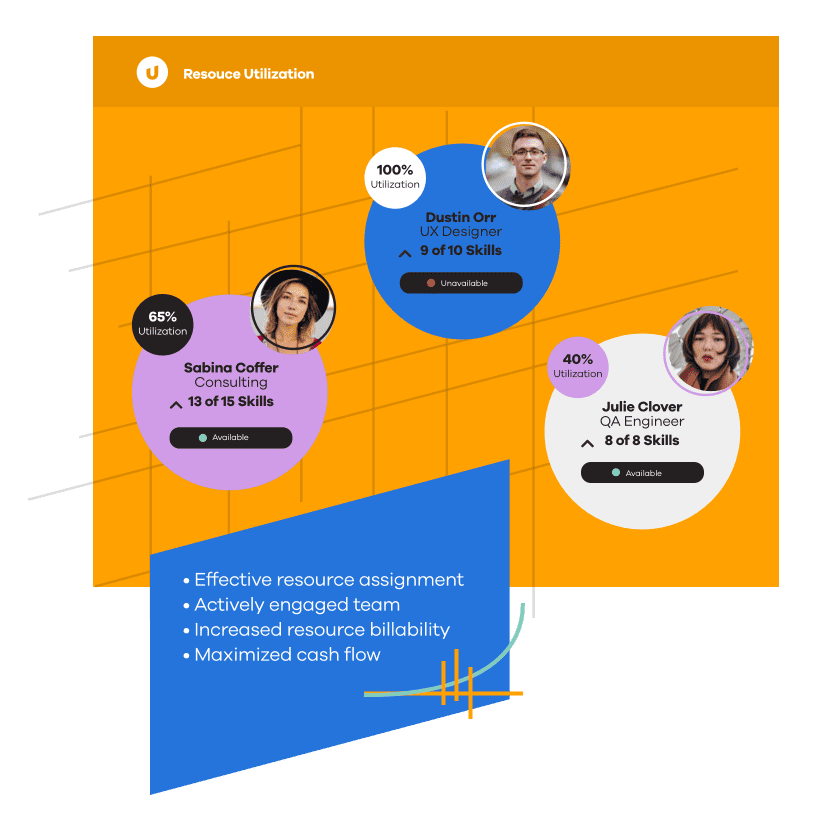
There are several key types of resources involved in the realm of resource utilization:
1. Human Resources
These are the skills, expertise, and efforts contributed by individuals within an organization or project. Effective allocation of human resources involves matching the right people to the right tasks, ensuring their capabilities are utilized optimally.
Managing workloads, fostering collaboration, and providing opportunities for skill development are all essential aspects of efficient human resource utilization.
2. Financial Resources
Financial assets represent a critical resource that guides the allocation of funds to various projects. Resource utilization involves prudent budgeting, investment decisions, and financial planning to drive sustainable growth.
Proper management of financial resources involves ensuring that an organization’s funds are allocated properly. This involves giving sufficient yet limited financial resources to initiatives that align with a strategic goal(s). In turn, it should deliver the highest return on investment.
3. Material Resources
Tangible assets, materials, and equipment constitute essential resources for manufacturing, construction, and various operational activities. The efficient use of these materials involves inventory management, minimizing waste, and optimizing production processes.
Effective resource utilization in this category is aimed at ensuring that all the materials and material-associated labor is utilized efficiently. It should reduce costs, minimize environmental impact, and limit liability at the same time.
4. Time Resources
Effective time management involves Setting priorities, scheduling tasks, and ensuring that deadlines are met without compromising quality.
Proper resource utilization of time involves eliminating inefficiencies, avoiding multitasking, and allocating time to tasks based on their importance and urgency.
5. Technological Resources
In today’s digital age, technological assets play a pivotal role in resource utilization. This includes software, hardware, data analytics tools, and automation technologies. Leveraging technological resources involves integrating them into processes to streamline operations, enhance decision-making, and drive innovation.
Resource utilization is one of the primary factors that contribute to operational success. When resources are allocated efficiently, waste is minimized, and productivity is maximized. Proper resource utilization enhances an organization’s ability to meet objectives, deliver value, and achieve strategic goals. It empowers decision-makers to make informed choices that drive growth and contribute to sustainable success.
The Intricacies of Efficient Resource Utilization
Resource utilization is akin to a dynamic and multifaceted orchestration. It is at the heart of modern endeavors. It involves balanced moves to address the demands of a rapidly evolving environment. Allocation and management of resources take center stage in almost every endeavor.
To balance supply and demand effectively, resource utilization strategically synchronizes together various components. These primarily include the five elements discussed in the previous section. Human capital, financial assets, materials, time, and technology seamlessly integrate to construct a productive framework.
Similar to a navigating through shifting waters, decision-makers rely on real-time data and insights. These insights can be gained beforehand to ensure proper resource utilization. Furthermore, market trends, customer behaviors, and operational metrics provide the compass points guiding resource allocation choices.
This shows a need for agile adaptation for proper resource utilization. It requires the flexibility of an adept problem-solver addressing unexpected challenges. Timely adjustments in allocation steer organizations through evolving landscapes, ensuring alignment with overarching objectives.
Challenges of Optimal Resource Utilization
While resource utilization serves as a vital compass for operational success, it navigates a landscape riddled with challenges. The art of effective resource allocation is not without its complexities, it requires you to address a range of obstacles. Let’s delve into some of them:
1. Competition for Limited Resources:
In a world of finite resources, organizations often find themselves in a fierce competition for the same pool of assets. This scenario amplifies the importance of strategic allocation to ensure that resources are optimally directed toward initiatives that yield the highest returns.
2. Changing Priorities:
The dynamic nature of business environments introduces shifts in priorities. New opportunities, market fluctuations, or unforeseen crises can lead to sudden changes in the allocation landscape. Navigating these shifts requires agility to swiftly realign resources.
3. Uncertainty & Risk:
Resource allocation decisions are fraught with uncertainty. Forecasting future demand, market trends, and operational challenges is an intricate task. Making the wrong allocation decisions can lead to wastage, missed opportunities, or operational disruptions.
4. Balancing Short-Term & Long-Term Goals:
Striking the right balance between short-term needs and long-term strategic goals is a constant juggling act. Focusing too heavily on immediate gains might neglect investments critical for sustained growth.
5. Data Complexity & Analysis:
Effective resource utilization relies on data-driven insights. However, the volume and complexity of available data can overwhelm decision-makers. Analyzing and interpreting data to inform allocation decisions can be a daunting task.
6. Organizational Silos:
Large organizations often operate in silos, where different departments or units have their resource allocation processes. This fragmentation can hinder efficient resource allocation across the entire organization.
7. Resistance to Change:
Implementing changes to resource allocation strategies may encounter resistance from employees accustomed to existing practices. Navigating this resistance requires effective change management and communication.
8. Suboptimal Allocation:
Misallocation of resources can lead to inefficiencies, reduced productivity, and missed growth opportunities. Ensuring that resources are directed where they can have the most significant impact is an ongoing challenge.
9. Technological Integration:
Incorporating technology for data analysis, predictive modeling, and real-time insights presents both opportunities and challenges. Implementing and integrating these technologies seamlessly requires strategic planning and expertise.
10. Regulatory & Ethical Considerations:
Certain industries operate under strict regulations or ethical guidelines that impact resource allocation. Navigating these considerations adds an extra layer of complexity to the process.
On the journey of optimizing resource utilization, addressing these challenges becomes paramount. Each obstacle presents an opportunity for organizations to refine their resource allocation strategies, enhance decision-making processes, and weave a tapestry of efficiency amidst complexity.
Breaking Down Resource Utilization Metrics
Understanding how well resources are being used in an organization is like solving a puzzle with various pieces. These pieces, which we call metrics, provide us with valuable insights into how efficiently resources are being employed to accomplish tasks.
Let’s take a closer look at the numbers:
1. Utilization Rate:
The utilization rate helps us understand whether a resource is being heavily used or if it’s spending more time idle. It’s like looking at how often a tool is in action compared to the total time it’s available.
For example, if a factory machine is running most of the time, its utilization rate is high. But if it’s sitting unused for long periods, the rate drops. It is calculated using a simple formula:
Utilization Rate = (Actual Usage Time / Total Available Time) x 100
Now, let’s imagine a delivery truck named “Speedy Hauler.” Over the course of a month, the truck was in operation for 600 hours out of a total of 720 hours. Applying the formula:
Utilization Rate = (600 hours / 720 hours) x 100 = 83.33%
This means that the “Speedy Hauler” truck was utilized at an 83.33% rate during that month. In other words, it was active and productive for about 83.33% of the time it was available.
2. Efficiency Rate:
Efficiency is all about how well a resource is performing its job. This metric considers both the quantity and quality of work. For instance, if a team is producing a large number of products, but those products often have issues, the efficiency rate might indicate room for improvement.
This metric is calculated using the following formula:
Efficiency Rate = (Actual Output / Expected Output) x 100
Imagine a manufacturing plant that produces bicycles. In a day, the plant is expected to produce 100 bicycles, but due to various factors like machine breakdowns and workforce issues, only 80 bicycles are manufactured. Applying the formula:
Efficiency Rate = (80 bicycles / 100 bicycles) x 100 = 80%
This means the manufacturing plant operated at an efficiency rate of 80% for that day. In simpler terms, it achieved 80% of its expected output due to the challenges it faced.
3. Capacity Utilization:
Imagine a hotel with many rooms. Capacity utilization reveals how many rooms are actually occupied in comparison to the total number available. If most of the rooms are filled, the utilization is high. But if a significant number of rooms are vacant, the utilization rate is lower.
The formula for capacity utilization is:
Capacity Utilization = (Actual Output / Potential Output) x 100
For example, imagine a call center with the capacity to handle 1000 customer calls per day. However, due to staffing shortages and technical issues, only 800 calls are attended to. Using the formula:
Capacity utilization = (800 calls / 1000 calls) x 100 = 80%
In this scenario, the call center is operating at a capacity utilization of 80%. This means that it is using only 80% of its full potential. The remaining 20% represents untapped capacity that could be utilized with improvements in staffing or technology.
Capacity utilization is like measuring the water level in a glass – it tells you how much of the glass’s capacity is currently filled. This metric guides organizations in making decisions about resource allocation and investment to achieve optimal utilization levels.
4. Resource Allocation Index:
This is a comprehensive metric that sheds light on whether resources are being distributed fairly across different groups or departments. It helps identify any imbalances, ensuring that no team is consistently getting more resources than they need while others struggle.
This metric takes into account multiple factors, including:
- Resource availability,
- Utilization rate, and
- Efficiency rate
While there isn’t a specific formula for this index, it involves a combination of key performance indicators to create a composite measure.
Imagine you’re managing a manufacturing plant that produces electronic devices. The plant has a certain number of workers, production machines, and raw materials. To calculate the Resource Allocation Index, you would assess:
- Utilization Rate of Workers: Are all workers engaged in productive tasks or is there idle time?
- Utilization Rate of Machines: Are the production machines operating at full capacity or experiencing downtime?
- Efficiency Rate: How efficiently are workers and machines converting raw materials into finished products?
- Resource Availability: Do you have the right number of workers and machines available for the level of demand?
Suppose your plant has a utilization rate of 90% for workers, 80% for machines, and an efficiency rate of 85%. Additionally, due to a shortage of certain raw materials, your resource availability is at 95%. To calculate the Resource Allocation Index, you’d factor in these values along with their respective weights or importance.
Resource Allocation Index = (0.3 * Utilization Rate of Workers) + (0.3 * Utilization Rate of Machines) + (0.2 * Efficiency Rate) + (0.2 * Resource Availability)
Using the provided example values:
Resource Allocation Index = (0.3 * 0.9) + (0.3 * 0.8) + (0.2 * 0.85) + (0.2 * 0.95) ≈ 0.855
In this hypothetical scenario, the Resource Allocation Index is approximately 0.855, indicating that the resource allocation and utilization are relatively effective, with room for further improvement.
The Resource Allocation Index is like a composite scorecard that considers various aspects of resource management, offering a nuanced understanding of how well an organization is utilizing its resources to achieve its objectives.
5. Workload Distribution:
Workload distribution ensures that tasks are evenly spread among team members. This maintains a balanced workload, preventing individuals from feeling overwhelmed and helping teams remain productive and content.
Imagine you’re managing a customer support team for an e-commerce company during the holiday season. The workload is expected to be significantly higher due to increased sales and customer inquiries. You have a team of 10 customer support agents available to handle customer interactions.
To calculate workload distribution, you would assess:
- Number of Tasks: Count the total number of customer inquiries or tasks that need to be addressed during a specific period, let’s say a day.
- Number of Resources: Determine the number of available customer support agents.
Suppose there are 300 customer inquiries expected in a day, and you have 10 customer support agents.
Workload Distribution = Number of Tasks / Number of Resources
Workload Distribution = 300 / 10 = 30
In this example, the workload distribution would be 30 customer inquiries per customer support agent. This means each agent is expected to handle approximately 30 tasks throughout the day.
However, you notice that certain agents are consistently handling more inquiries than others. Some agents are dealing with 40 inquiries while others are managing only 20. This imbalance indicates an uneven workload distribution, which could lead to burnout for some agents and potential delays in addressing customer issues.
To improve workload distribution, you might redistribute tasks based on agent skills and availability.
6. Resource Turnover:
Think of resource turnover as the cycle of usage and replenishment. It gauges how quickly a resource is consumed and then made available again. A swift turnover suggests efficient use and readiness for the next task.
Let’s say you’re managing a manufacturing plant that produces electronic devices. One of the key resources in your production process is a specialized machine used for soldering components onto circuit boards. This machine is critical to your production line, and downtime can lead to delays and decreased output.
To calculate resource turnover for the soldering machine, you would assess:
- Number of Uses: Count the total number of times the soldering machine is used for soldering tasks within a specific period, let’s say a month.
- Total Available Machines: Determine the total number of soldering machines you have in your production facility.
Suppose the soldering machine is used 500 times in a month, and you have 2 soldering machines.
Resource Turnover = Number of Uses / Total Available Machines
Resource Turnover = 500 / 2 = 250
In this example, the resource turnover for the soldering machine would be 250. This means the machine is being utilized and replaced approximately 250 times within a month.
As you analyze this metric over several months, you notice a trend: the resource turnover for the soldering machine has been consistently high. This indicates that the machine is frequently used and replaced, which could raise concerns about its longevity and potential maintenance needs.
7. Opportunity Cost:
Opportunity cost guides decision-making regarding resource allocation. It prompts us to consider what we might miss out on when we choose one option over another. For instance, if we invest funds in one project, we might forgo the chance to fund another project with potentially greater benefits.
In this example, you’re the manager of a software development team, and you have a team of skilled programmers who can work on different projects simultaneously. You have two potential projects: Project A, which involves developing a new innovative software product, and Project B, which is an enhancement to an existing software application.
Let’s assume the following potential outcomes for each project:
Project A:
- Estimated Revenue: $100,000
- Development Time: 3 months
Project B:
- Estimated Revenue: $60,000
- Development Time: 2 months
Now, let’s consider the opportunity cost of choosing to allocate your team’s resources to Project A over Project B. The opportunity cost is the potential revenue that you forego by not choosing the alternative with the highest return.
Opportunity Cost = Revenue of Next Best Alternative – Revenue of Chosen Alternative
Opportunity Cost = $60,000 (Project B’s revenue) – $100,000 (Project A’s revenue) = -$40,000
In this scenario, by choosing to allocate your team’s resources to Project A, you are forgoing potential revenue of $60,000 that could have been earned by working on Project B. The negative value indicates that Project A is less financially rewarding compared to the next best alternative. While Project A might seem more lucrative at first glance, considering the opportunity cost reveals that Project B offers a higher return on investment in terms of revenue per unit of time.
These metrics provide diverse perspectives on resource usage. By analyzing them, organizations can make more informed choices about where to allocate their resources and how to maximize their effectiveness. It’s like having a toolkit that helps us use resources wisely and efficiently.
Wrap-up
Resource utilization is the compass guiding industries toward efficiency and success. It involves managing a wide spectrum of assets, from human capital to intangible dimensions like time and expertise. As technology reshapes the landscape, strategic resource allocation becomes paramount. Resource utilization isn’t just a concept; it’s transformative, shaping productivity, innovation, and resilience. By mastering this art, businesses can navigate challenges toward sustainable growth and accomplishment.