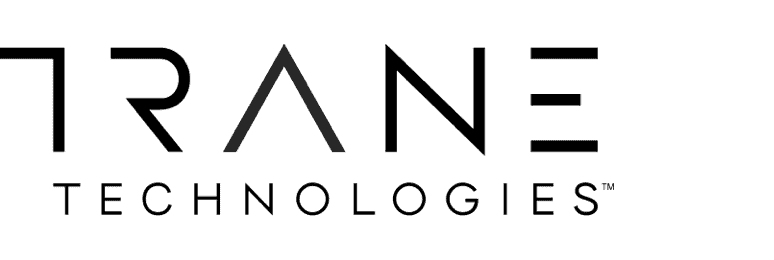
How Trane Technologies reduced 25% in inventory costs using Ultriva
How Trane Technologies reduced 25% in inventory costs using Ultriva
Learn how Trane Technologies used Ultriva to reduce inventory costs, gain control over its supply chain operations, and improve collaboration with partners.